-
-
Hydraulic Breaker ChiselForging type II
The tip forging tool is suitable for soft and sandy geology.
GUIDE TO THE CORRECT
USE OF BREAKER CHISELS
-
01
Before installing the breaker chisel,apply an appropriate amount of grease. Make sure that the correct high-quality grease is properly flled before work and added regularly during work.
-
02
Regularly check the wear of the guide bushings and fixing pins of the breaker chisel. When the wear tolerance exceeds the standard, it should be replaced in time, and always ensure that it has a good guiding/fixing effect.
-
03
Do not continuously strike at the same position for more than the operating time recommended by the breaker manufacturer, usually up to 10-15 seconds.
-
04
Before starting the breaker, make sure that the working end of the chisel is in full contact with the working surface. Stop striking immediately after successful crushing to avoid empty strikes.
-
05
Make sure that the breaker chisel is always applied to the working surface at a right angle (90 degrees). The correct working angle is the key to ensure the service life of the chisel and other related parts.
-
06
When the working end of the breaker chisel is damaged or worn to the point of losing its original performance, it is recommended to trim it by miling, planing or turning (in most normal cases, the chisel does not need to be repaired).
-
07
Check the breaker guide bushings/ pins and chisel surface regularly for possible chips or cracks (these marks indicate improper use of the breaker or poor quality of related accessories), and grind the surface into visible finishing with the help of a grinding wheel.
-
08
When the striking position needs to be changed during operation, do not try to pry the breaker hard, but gently shake the breaker towards the operating room to reduce the accumulation of powder around the working end of the chisel.
GET TO THE ROOT The main stresses of breaker chisels: When the hydraulic breaker is used improperly, these stresses will combine and increase significantly. A sharp increase in one of the following stresses or a combination of different types of stresses may lead to fatigue failure of the breaker chisel.
OF THE PROBLEM
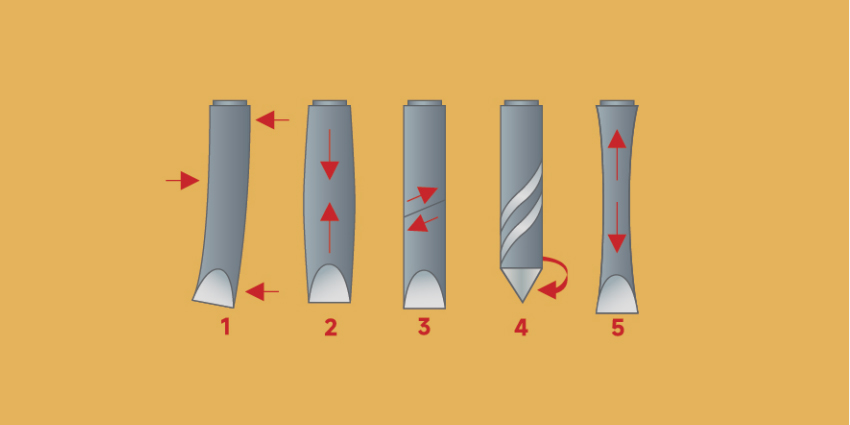
1. Bending stress
2. Compressive stress
3. Shear stress
4. Torsional stress
5. Tensile stress
TYPICAL FAILURES Yulindingli breaker chisels are manufactured with 100% independent technology and strict quality control (ISO9001:2015 certified) to ensure that the chisels have excellent characteristics such as optimal fatigue resistance and wear resistance. When a failure occurs, a simple visual inspection can usually quickly identify the cause. Contact us to obtain Yulindingli's detailed warranty claim guide PDF.
(WARRANTY CLAIM GUIDE)